How AI Agents Automate Manufacturing Facility Capacity Planning for Operations Directors
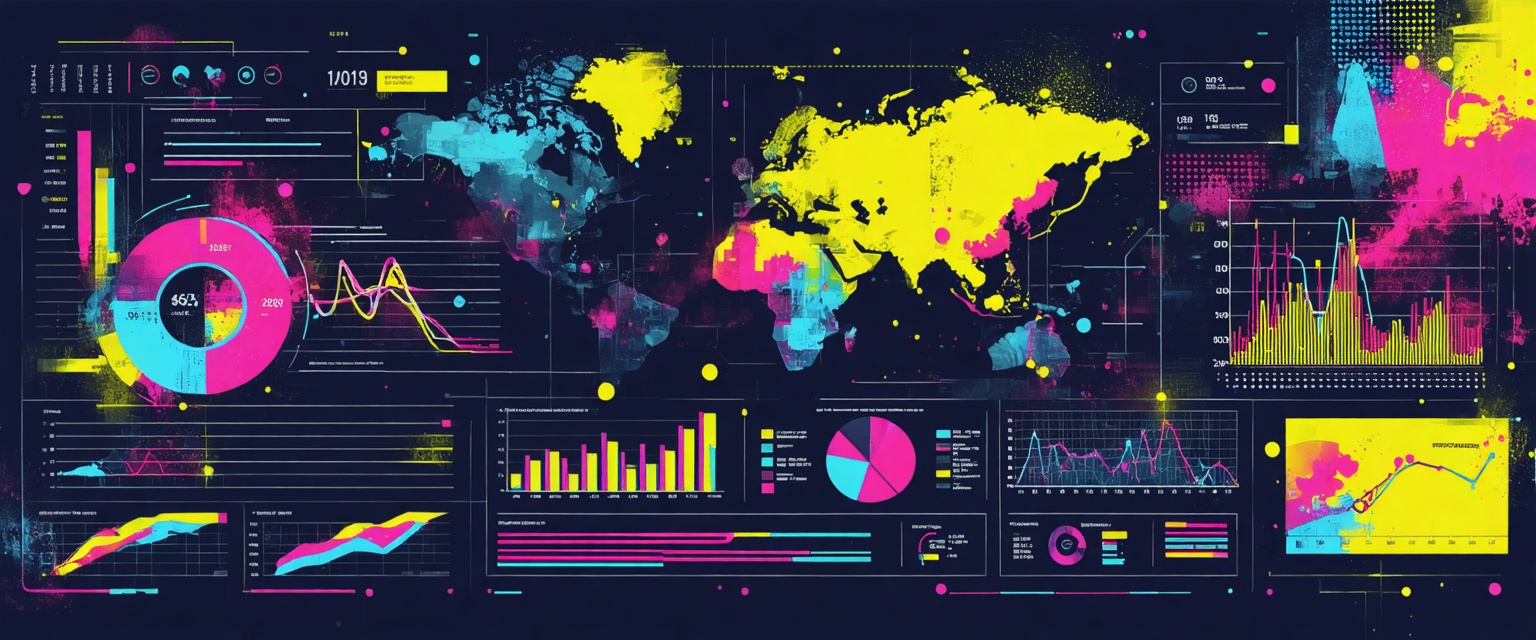
Discover how AI agents revolutionize capacity planning for Operations Directors. Enhance efficiency, spot bottlenecks, and optimize resource allocation.
Operations directors still rely on patchy data and spreadsheets to plan capacity. That’s why equipment sits idle, delays stack up, and customers start looking elsewhere. The real problem? Your systems don’t talk to each other.
With Agentic AI, you can now bring those siloed systems together and act on your data in real time.
Datagrid’s data connectors plug into your existing systems and give AI agents full visibility into machine usage, labor, inventory—so they can flag bottlenecks and adjust schedules on the fly. This article highlights what you can automate today and how to start seeing results fast.
Why AI Agents Matter for Operations Directors in Manufacturing Capacity Planning
For operations directors, AI agents deliver instant, data-backed insights that traditional methods simply can't match in automating manufacturing facility capacity planning.
These systems constantly monitor your constraints—equipment availability, worker schedules, downtime patterns—then propose or execute production adjustments in real time. This approach gives manufacturers unprecedented flexibility in responding to challenges.
Real-Time Adaptability
AI agents process information continuously, unlike static spreadsheets or periodic ERP updates. When a supplier experiences issues, the AI immediately recalibrates production schedules to minimize disruption. You can even use Calendly with AI agents to enhance scheduling efficiency.
Enhanced Forecast Accuracy
AI algorithms identify subtle patterns in historical and current data that human planners cannot detect. Studies show that AI-driven forecasting can achieve up to 97% accuracy, compared to only about 50% for traditional methods based on historical averages.
Optimized Resource Allocation
By understanding the relationships between all production factors, AI agents precisely allocate labor, equipment, and materials, reducing waste and improving output.
Scenario Planning
AI agents run simulations to help operations directors prepare for potential disruptions before they occur, an essential capability in manufacturing.
Here's what this looks like in practice:
- When detecting a sudden demand spike, an AI agent automatically adjusts schedules, reallocates resources from less urgent items, and recommends temporary staffing increases, perhaps even helping to utilize AI agents for lead generation.
- By monitoring equipment sensor data, AI can predict machine failures and suggest preventive maintenance during planned downtime periods.
- If the system detects supply chain issues through supplier data or external events, it can propose alternative sourcing options to maintain production continuity.
Common Time Sinks in Traditional Manufacturing Facility Capacity Planning
Traditional capacity planning methods create numerous inefficiencies for operations directors:
Reliance on Static Excel Sheets and ERP Snapshots
Many factories still depend on outdated spreadsheets or ERP data, resulting in:
- Decisions based on outdated information
- Hours spent on manual data entry
- Undetected errors affecting production
Production planners often dedicate entire days to collecting and validating data rather than making strategic decisions, highlighting the need to ensure data quality with AI.
Delays in Information Flow
The lag between sales forecasts and production updates creates:
- Misalignment between customer demand and production output
- Reactive problem-solving instead of proactive planning
- Missed opportunities to adapt to market changes
Manual Reconciliation of Capacity Across Operations
Production planners waste valuable time adjusting schedules because:
- Capacity varies significantly across shifts, lines, and facilities
- Workloads require constant manual balancing
- Visualizing total capacity utilization is challenging
A typical scheduler at a mid-sized manufacturer might spend 15+ hours weekly just reconciling capacity across three production facilities.
Late Visibility of Resource Bottlenecks
Traditional methods often identify resource constraints too late, forcing:
- Emergency production schedule adjustments
- Hasty resource reallocation
- Disrupted workflows
Consequences of These Time Sinks
These inefficiencies lead to serious operational issues:
- Overstaffing: Lack of real-time data results in excessive labor scheduling and increased costs.
- Underutilized Machines: Without dynamic resource allocation, expensive equipment remains idle while bottlenecks form elsewhere.
- Missed Orders: Inability to adjust quickly leads to disappointed customers and lost business.
- Overtime Costs: Last-minute adjustments require expensive overtime hours.
- Inventory Imbalances: Poor alignment between capacity and demand creates either excess stock or shortages.
AI Agent Applications in Automating Manufacturing Facility Capacity Planning
AI agents have several use cases in manufacturing facility capacity planning. Here are some common applications:
Real-Time Data Integration and Anomaly Detection
AI agents connect data from your ERP, MES, SCADA, and IoT sensors in real time. This comprehensive view enables automatic detection of issues that could impact facility capacity. Moreover, businesses can automate social monitoring to stay ahead of market trends.
These systems process massive data flows and continuously update planning parameters. An AI might identify a slight increase in assembly time that could create a bottleneck, allowing your team to address it before production is affected.
For example, AI can detect supply problems by connecting supplier delivery patterns with production schedules, providing planners with advance notice to make adjustments.
Dynamic Resource Allocation and Production Scheduling
AI agents assign resources based on current shop floor conditions, incoming orders, and operational constraints. This shifts planning from rigid charts to adaptive schedules that evolve as conditions change, enabling companies to automate campaign reports and focus on strategic tasks.
When urgent orders arrive or equipment malfunctions, AI quickly recalculates optimal schedules. These systems evaluate multiple scenarios, considering factors like overtime costs versus late deliveries, and recommend the most effective approach.
This allows schedulers to focus on reviewing AI recommendations and making strategic decisions rather than manual spreadsheet adjustments.
Predictive Maintenance and Constraint Management
AI uses sensor data and maintenance history to forecast equipment failures and recommend maintenance windows that minimize production disruption. By incorporating machine health into planning models, these systems adjust output expectations based on early warning indicators, much like predictive lead scoring with AI enhances sales processes.
ThroughPut AI's capacity planning software exemplifies this approach by tracking asset performance and enabling scenario planning. Their system aligns demand and capacity in real time, reducing costs and improving asset utilization.
With these AI capabilities, manufacturers achieve greater flexibility and efficiency, transforming capacity planning from a reactive process into a strategic advantage.
Datagrid for Operations Directors in Manufacturing
Datagrid's AI platform offers targeted solutions for operations directors facing data management challenges:
Supply Chain Documentation Management
Our AI processes thousands of supplier specifications, BOMs, and compliance certificates simultaneously. It extracts critical details to maintain visibility across your supply network, reducing manual processing time by up to 80%.
Quality Control Automation
Datagrid examines production data, testing reports, and defect documentation to identify patterns and predict quality issues before they occur. A food manufacturer using our system reduced quality incidents by 35% by detecting subtle patterns in production line data.
Regulatory Compliance Support
Our AI agents track changing regulations and automatically identify compliance gaps in your documentation. A medical device manufacturer using Datagrid successfully passed three consecutive audits without penalties.
Equipment Maintenance Optimization
Datagrid extracts insights from maintenance logs, equipment manuals, and performance data to predict maintenance needs. An automotive parts supplier reduced unplanned downtime by 42% with our predictive maintenance capabilities.
Production Workflow Analysis
Our platform analyzes production reports across multiple facilities to identify bottlenecks and efficiency opportunities. A multi-site manufacturer discovered a 23% throughput improvement by analyzing cross-facility patterns with Datagrid.
Product Specification Management
Datagrid automatically extracts and organizes technical specifications from various document formats. This helped an electronics manufacturer reduce new product introduction time by three weeks by eliminating manual specification reviews.
Datagrid integrates with your existing systems, complementing your Manufacturing Execution Systems (MES), Enterprise Resource Planning (ERP), and other operational technologies to:
- Automate tedious data processing tasks
- Generate actionable insights from unstructured data
- Improve decision-making with real-time analytics
- Enhance cross-departmental collaboration
- Reduce documentation errors
Our platform even allows you to optimize data with AI agents, ensuring your organization makes the most of its data assets.
Simplify Manufacturing Facility Capacity Planning with Datagrid's Agentic AI
Don't let data complexity slow down your team. Datagrid's AI-powered platform is designed specifically for teams who want to:
- Automate tedious data tasks
- Reduce manual processing time
- Gain actionable insights instantly
- Improve team productivity
See how Datagrid can help you increase process efficiency.
Create a free Datagrid account.